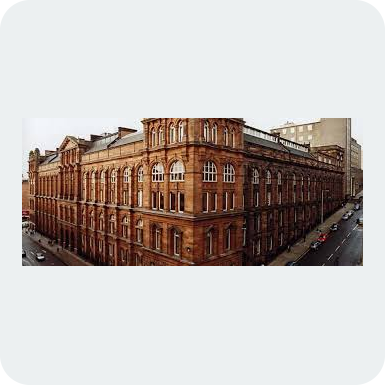
Strathclyde University:
"We are hosting an event of cryogenic propulsion next Wednesday at Strathclyde University.
https://www.eventbrite.co.uk/e/cryogenic-propulsion-technology-for-next-... "
Description
Two speakers from Rolls Royce Electric will present the latest technology on cryogenic propulsion for electric aircraft.
10:00-10:45 Presentation one: CEPS- A cryogenic electric propulsion system for short range aircraft
Abstract: Currently hybrid-electric aircraft are under investigation as one possible solution to reduce the emissions of the aviation industry according to the Flightpath 2050 of the European Union. To meet the drive train’s requirements on smallest mass while aiming for highest efficiency, superconducting technologies are regarded as a key enabling technology for drive train powers of several tens of megawatts. Within the German nationally funded project TELOS an exemplary mission profile of a 200-passenger aircraft is used to derive the requirements for a cryogenic cooled hybrid-electric propulsion system (CEPS). To optimize the total system performance, we subsequently evaluated the superconducting and cryogenic cooled components by using computationally fast, analytical models. This approach allows to quantify the system performance by using component technologies being available today and formulating required technological developments in the field of applied superconductivity for the future.
10:45- 11:00 Q&A, tea break
11:00-11:45 Presentation two: Reimagining design and manufacturing aspects of electric, superconducting and cryogenic components for aircraft
Abstract: A major technical challenge is to find a safe and profitable concept for a MW-class, hybrid-electric propulsion system for a commercial aircraft in order to reduce emissions and noise according to the Flightpath 2050 of the European Union. Superconducting and cryogenic electrical systems have been identified as key technologies for achieving to achieve maximum efficiency while minimizing the total weight of all components. We have developed a resilient design of a 10 MW generator using DC coils made of 2G HTS to provide a new technology for motors and generators with power densities above 20 kW/kg. This includes the identification and validation of lightweight materials for all parts of the generator that meet the thermal, electrical, mechanical and compatibility requirements for cooling with LH2. We have also carried out manufacturing and assembly tests to check material availability and feasibility. To optimize our multi-physics model of the generator during the design process, we subsequently updated the design and material databases using our test results. This approach enabled us to gain considerable insight at a very early stage (proof of concept) of technology development. In addition, the system pre-development tools could be adapted immediately, thus avoiding undesirable developments.
11:45-12:00 Q&A
Presenter 1:
Martin Boll studied physics (diploma) with the focus on quantum many body systems in Mainz (07-11). Joining Max-Planck Institute and University of Munich, Martin worked on charge and spin resolved microscopy for quantum simulators, receiving his PhD in 2016. He switched to industry at Siemens eAircraft in Germany, focussing on the development of hybrid-electric drive trains for aircraft in the megawatt power range. After turning to Rolls Royce Electrical in 2019, he is currently employed as technical project manager and system architect working on subsystem and component modelling of superconducting and conventional electric drive trains.
Presenter 2:
Lars Kuehn studied electrical engineering (diploma) with a focus on electrical machines and drives in Dresden (98-02). Subsequently, he worked as a Researcher at the University of Applied Science Dresden (03-05) focusing on linear motors, power trains and vehicle electrical systems. He moved to the Leibniz Institute for Solid State and Materials Research and the Technical University Dresden in 2009. Lars worked on unconventional superconductors as high-Tc cuprates and their use in motors, bearings, medical devices and innovative transport systems. Lars received a second engineering diploma in electrical transportation systems followed by his PhD. In 2009 he was hired by the start-up “evico” to establish the business unit “Superconducting Materials, Magnets & Applications”. After running a successful business unit for seven years, Lars moved to Siemens in Munich (2016) and took over the responsibility for the development of a 10 MW HTS generator for aircraft in the mega watt power range. Since April 2019, Lars has held the position of Chief Engineer, responsible for the development of hybrid-electric powertrains for regional aircraft – and since October 2019 employed by Rolls Royce.
Click https://www.eventbrite.co.uk/e/cryogenic-propulsion-technology-for-next-... for more information